Child labor and collapsing tunnels in DR Congo's cobalt mines are bringing electric cars and other vehicles into disrepute. But the push for transparency along the country's cobalt supply chain is met with resistance.
Mining engineer Pierre Amani Kangenda peers into the mouth of a narrow shaft that plunges straight down to the belly of a cobalt mine.
He can't quite make out the silhouettes of the young men whose job is to heave 20-kilogram (44-pound) sacks of dirt rich in cobalt and copper composite up the mine wall to the surface. But he can see their headlamps in the darkness.
The men use pickaxes and shovels to dig for cobalt in this small-scale mine known as UCK Drain on the outskirts of Kolwezi in the DRC's southern copper belt, where great amounts of cobalt are mined.
"As soon as they reach the vein of ore, they start extracting the raw materials," says Kangenda who is decked out in a high-visibility vest as he conducts his daily patrol of the site which has 59 shafts.
"When they reach a depth of 30 meters (98 feet), they stop and look for another place to dig. That's what the rules [on this site] say."
Elsewhere, shafts can sink as deep as 100 meters, depending on local regulations.
Large informal mining sector
The Democratic Republic of the Congo accounts for some two-thirds of the world's cobalt, dwarfing the output of its closest competitors, Australia and Russia. Around 15-20% of Congo's cobalt supply is dug up by artisanal miners like those working here at UCK Drain.
Tunneling deep into the red dirt is hard and dangerous work. However, it's somewhat safer here than at other artisanal mines in the country.
That's because Kangenda, who works as a monitor and trainer for RCS Global, a consultancy with a focus on supply chain transparency and responsible sourcing, is there to make sure of standards being upheld.
"I check what problems there are. Are there children on site? Is there violence and rape?" he tells DW.
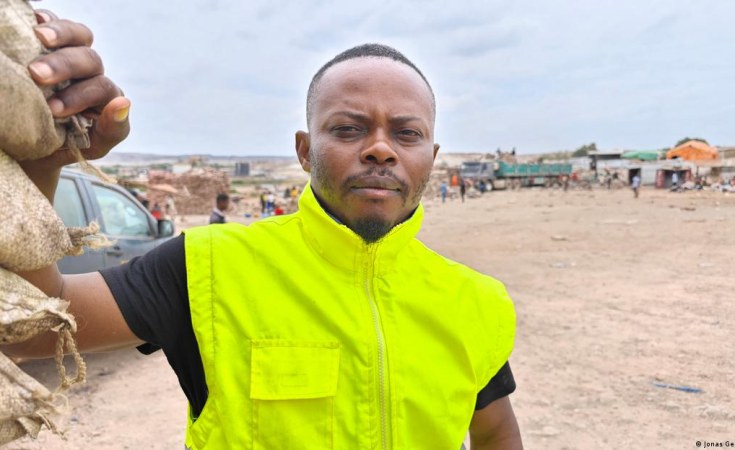
The tunnels must be secured and closed down if cracks appear, Kangenda explains, and corrugated iron roofs over the shafts are erected to protect them from rain. Pregnant women and military personnel aren't allowed on the site.
"If there are incidents, we report them to our partners. We try to correct them so that the supply chain is internationally acceptable," Kangenda explains.
Saving the reputation of e-mobility
Kangenda documents everything he observes on his patrols into a computer program. The mine is one of eight that are part of RCS's Better Mining program, which aims to continuously monitor and support the improvement of conditions on and around artisanal and small-scale mine sites.
Partner companies along the supply chain can view the data logged in the program and react to it. This is important as the demand for cobalt continues to skyrocket.
Cobalt is a key component of rechargeable lithium-ion batteries that power electronic devices and electric vehicles (EVs). But reports of dangerous working conditions and child labor in Congo's informal mines have sparked an outcry over what has been referred to as "blood cobalt" in recent years.
This is forcing EV manufacturers, who market themselves as sustainable, to look for ways to source 'clean cobalt' untainted by abusive labor practices. This is proving a difficult undertaking.
Stopping child labor in all forms
Because of the monitoring of this mine, it's relatively easy to ban children from working in the tunnels or even from entering the actual mining site.
But it's more difficult to stop children selling the raw ore they find by sifting through rock scraps on-site to the Chinese middlemen who control the majority of the trading depots.
"We try to explain to the depot owners that they are not allowed to buy the raw materials brought to them by children," says Kangenda. "That is the condition we impose on them."
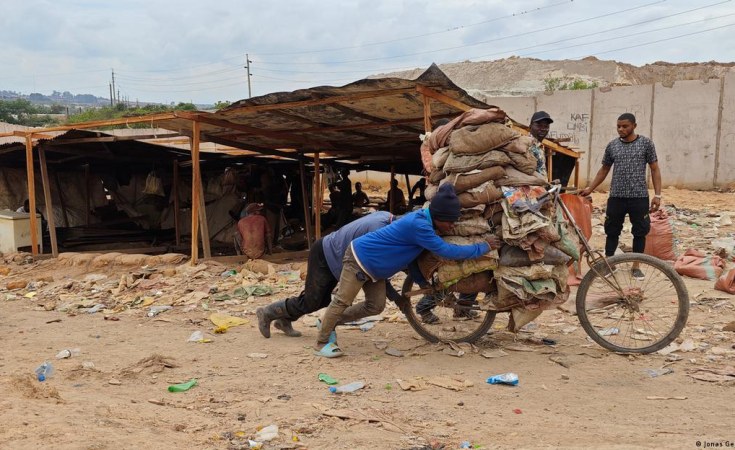
Better Mining has also launched information campaigns in the surrounding schools and churches to try to keep children away from the mine site.
"We are thinking about how we can cordon off the site," says Alain Mpalanga, the deputy head of the Somikas' cooperative, which organizes UCK miners.
"If we manage to do that, including the depots and the bistro area, then children will no longer have access."
The persistent issue of collapsing tunnels
Somikas earns 10% for every kilogram of copper and cobalt mined on the UCK Drain site, explains Mpalanga as he sits in his cramped office at the site entrance.
He oversees as many as 5,000 miners, who work on the site. They aren't formally employed. Rather, they work together to excavate a tunnel and pool their earnings.
Asked about RCS Global, Mpalanga says: "We work in symbiosis."
But the issue of death hangs over the mine's operations:
"There have been many deaths [from cobalt mining] since raw materials started being traded on a large scale," he tells DW. "But we have been able to put an end to the series of constantly collapsing tunnels because we now have technical experts and engineers."
That doesn't mean there are no more fatalities from collapsed tunnels. Rather, fewer people die when walls cave in, Mpalanga admits.
"We've never had more than five fatalities in one accident," he says, compared to incidents that have killed dozens at once.
Perfectly clean supply chain not yet possible
Better Mining isn't a certificate for a flawless supply chain. Rather, it's goal is to enable companies at the end of the supply chain to comply with corporate due diligence obligations abroad, such as is now required by German law, says Lucien Bahimba, a compliancy expert and RCS Global's regional coordinator.
"This is a continuous effort in which people come to understand that within perhaps a month or a year they have to abandon behaviors that they have been doing for five or ten years. It's not always easy," he says from his air-conditioned office in Kolwezi.
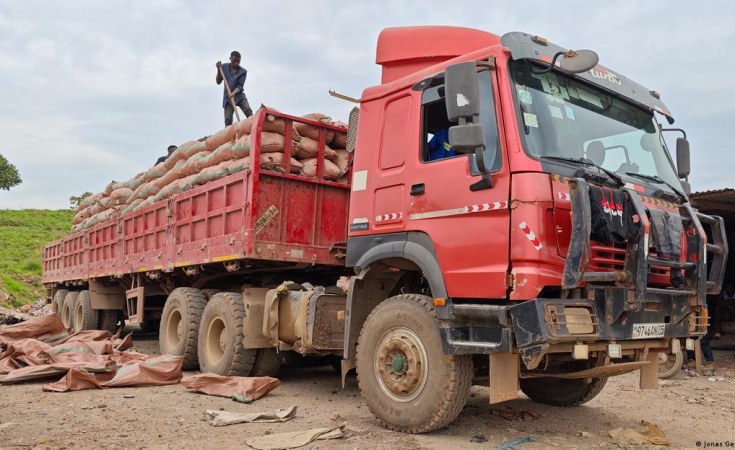
Bahimba points to his laptop screen, which shows the mines that are being monitoring. Each mine has a rating, and the program displays individual grievances as well as corrective measures that are pending as well as those that have already been implemented.
Companies at the end of the supply chain can also see this information. RCS Global has listed the car manufacturers Volvo, Ford and General Motors on its homepage as partners.
Sources mixed at the middlemen
Back at the mine, people push bicycles heavily laden with dusty sacks of ore up a hill to a row of wooden shacks spraypainted with the names of Chinese buyers. Inside these trading depots, the ore is broken up, assessed for purity and weighed.
A truck stands idle as workers load it with raw material to be taken to a plant for processing. This is a critical point in the supply chain.
"Our work is limited to providing information about the mines that we monitor," says Bahimba from RCS Global.
The problem, he says, is that the processors source their raw materials from several mines, and there simply is no knowing what the conditions are like at each one of them.
"The ore is mixed up," he says. "And that's still a bit of a concern in the copper and cobalt sector."
That means that Better Mining, and other similar transparency programs, can't stop raw materials obtained from problematic sources from entering the supply chain yet.
For this to happen, such programs would have to cover Congo's cobalt mines on a large scale and be backed up by actionable laws.
"That would actually be the ideal," Bahima says.
This article was originally written in German
Edited by: Sertan Sanderson